Micro Joining Equipment
Pioneer in Micro Joining Industry
Nippon Avionics is the world’s premier manufacturer of welding & micro joining equipment; pulsed heat and resistance welding technology as well as a leading supplier of laser welders and seam sealing equipment. We offer their entire line of equipment, which allows us to provide a complete solution to your hotbar welding, pulsed heat assembly, or sealing requirements. These are complex technologies, and we offer the units to be combined by an integrator into an assembly workstation and complete turnkey systems, both off-the-shelf and custom-designed for your application.
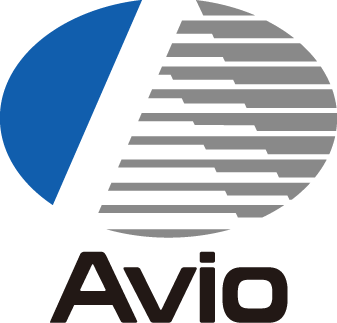
Nippon Avionics is the world’s premier manufacturer of welding & micro joining equipment; pulsed heat and resistance welding technology as well as a leading supplier of laser welders and seam sealing equipment. We offer their entire line of equipment, which allows us to provide a complete solution to your hotbar welding, pulsed heat assembly, or sealing requirements. These are complex technologies, and we offer the units to be combined by an integrator into an assembly workstation and complete turnkey systems, both off-the-shelf and custom-designed for your application.
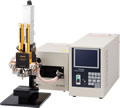
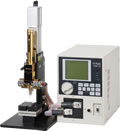
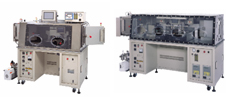
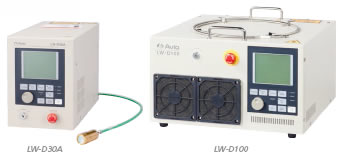
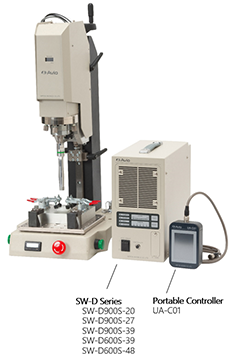
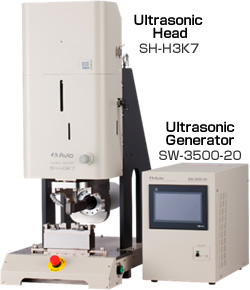
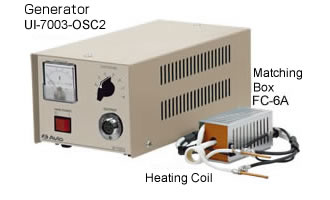
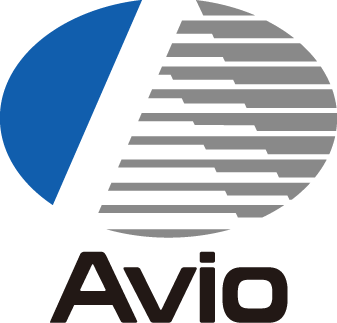
Resistance Welding
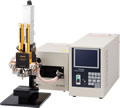
Resistance welding is a method in which the welding works are heated by resistance heat generated by sandwiching the welding workpieces with welding electrodes, passing current through them, and the metal is welded while pressurizing the works.
A resistance welding machine composed of welding power supply, a weld head and an electrode. The welding power supply controls a welding current, the weld head exerts a pressure on the material to weld and the electrode provides welding current and pressurization force to the part under welding. We have been providing various kinds of welding power supplies and welding heads to meet these requirements.
Pulse Heat Welding (Hot Bar Bonder)
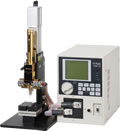
Pulse Heat is Avio’s original process of utilizing resistance heat which is generated by passing an electric current through a metal heating body called a heater chip/heater tool, to instantaneously perform soldering, thermos-compression bonding, and plastic welding with heat and pressure.
Pulse Heat is Avio’s original process of utilizing resistance heat which is generated by passing an electric current through a metal heating body called a heater chip/heater tool, to instantaneously perform soldering, thermos-compression bonding, and plastic welding with heat and pressure.
- The temperature rises quickly and the temperature reproducibility is good.
- Temperature profiles such as pre/main heat can be easily realized.
- Due to local heating, the heat effect to the surroundings is small.
- Since it is cooled while being pressed down, there is no unconnected due to floating.
- It does not depend on skill level of the worker.
Pulse Heat Welding (Hot Bar Bonder)
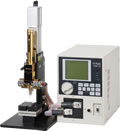
Pulse Heat is Avio’s original process of utilizing resistance heat which is generated by passing an electric current through a metal heating body called a heater chip/heater tool, to instantaneously perform soldering, thermos-compression bonding, and plastic welding with heat and pressure.
Pulse Heat is Avio’s original process of utilizing resistance heat which is generated by passing an electric current through a metal heating body called a heater chip/heater tool, to instantaneously perform soldering, thermos-compression bonding, and plastic welding with heat and pressure.
- The temperature rises quickly and the temperature reproducibility is good.
- Temperature profiles such as pre/main heat can be easily realized.
- Due to local heating, the heat effect to the surroundings is small.
- Since it is cooled while being pressed down, there is no unconnected due to floating.
- It does not depend on skill level of the worker.
Resistance Welding
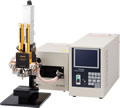
Resistance welding is a method in which the welding works are heated by resistance heat generated by sandwiching the welding workpieces with welding electrodes, passing current through them, and the metal is welded while pressurizing the works.
A resistance welding machine composed of welding power supply, a weld head and an electrode. The welding power supply controls a welding current, the weld head exerts a pressure on the material to weld and the electrode provides welding current and pressurization force to the part under welding. We have been providing various kinds of welding power supplies and welding heads to meet these requirements.
Parallel Seam Sealers
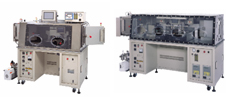
Optimum production corresponding to packages from Crystal,SAW,Optical device,Sensor,MEMS. Various lineup available for R&D and mass production.
It is a semi-automatic seam sealing equipment that hermetically seals packages such as crystal & SAW devices, optical devices, sensors, and MEMS in N2 atmosphere.
- Various Operation modes available for R&D and mass production.
- PKG size 2~150mm – Rectangular, round, polygon
- Easy Operation & Programming
- Automatic program verification
Laser Welder
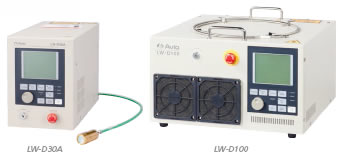
It is an equipment to solder or weld plastics by the laser beam. Micro joining is achieved by utilizing the high energy of a laser beam.
LW-D series of laser diode welders irradiates the laser emitted from the laser diode onto a plastic part and welds it in a non-contact manner. This is an air-cooled, compact laser welding machine that can be easy operation. It is most suitable for soldering and plastic welding.
- Applicable to Various Shapes and Material
- Three types of output mode are available(Profile, Continuous, Pulse)
- Laser Output Waveform is Visualized
- Preset numerical data is converted into waveform and displayed
- Actual output waveform is trace displayed
- Simple Operation
- Laser can be output immediately after switch ON
- Easy-to-operate jog dial is equipped
- Guide light to confirm laser output position is provided
- Suitable to be Equipped on Automated Machine
- RS-232C, I/O equipped
- Various monitoring (alarm) functions
- Desk Top Type
- Compatible to Pb Free Solder
Laser Welder
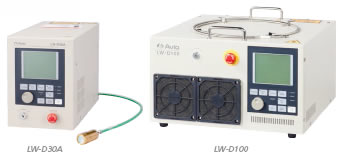
It is an equipment to solder or weld plastics by the laser beam. Micro joining is achieved by utilizing the high energy of a laser beam.
LW-D series of laser diode welders irradiates the laser emitted from the laser diode onto a plastic part and welds it in a non-contact manner. This is an air-cooled, compact laser welding machine that can be easy operation. It is most suitable for soldering and plastic welding.
- Applicable to Various Shapes and Material
- Three types of output mode are available(Profile, Continuous, Pulse)
- Laser Output Waveform is Visualized
- Preset numerical data is converted into waveform and displayed
- Actual output waveform is trace displayed
- Simple Operation
- Laser can be output immediately after switch ON
- Easy-to-operate jog dial is equipped
- Guide light to confirm laser output position is provided
- Suitable to be Equipped on Automated Machine
- RS-232C, I/O equipped
- Various monitoring (alarm) functions
- Desk Top Type
- Compatible to Pb Free Solder
Parallel Seam Sealers
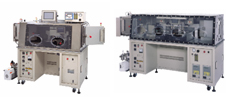
Optimum production corresponding to packages from Crystal,SAW,Optical device,Sensor,MEMS. Various lineup available for R&D and mass production.
It is a semi-automatic seam sealing equipment that hermetically seals packages such as crystal & SAW devices, optical devices, sensors, and MEMS in N2 atmosphere.
- Various Operation modes available for R&D and mass production.
- PKG size 2~150mm – Rectangular, round, polygon
- Easy Operation & Programming
- Automatic program verification
Ultrasonic Welding
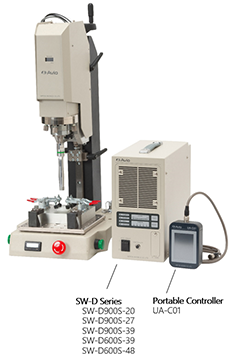
It is an ultrasonic plastic welder which utilizes ultrasonic vibration energy to perform secondary processing of plastic. It can be used not only for plastic welding but also for various purposes such as plastic caulking, fusing and cutting of non-woven fabrics, hood cutting, and packaging processing.
High-speed・automation machine type line up to support reliable “Monozukuri” (manufacturing)
SW-D series has 5 models of 20kHz~48.5kHz, 600W/900W with various control mode and monitoring function, which is applicable to wide variety of work. It is the high-end ultrasonic welder with Ethernet capability and tractability.
- The temperature rises quickly and the temperature reproducibility is good.
- Temperature profiles such as pre/main heat can be easily realized.
- Due to local heating, the heat effect to the surroundings is small.
- Since it is cooled while being pressed down, there is no unconnected due to floating.
- It does not depend on skill level of the worker.
Ultrasonic Metal Welding
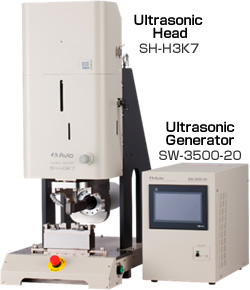
Ultrasonic metal welding method is used to join dissimilar metals of aluminum wire and copper for aluminum harnesses, thin copper alloys for vapor chambers and hoop materials, and aluminum laminated foil for rechargeable batteries
Highly Reliable Welding of Aluminum Cables to Copper Terminals
Welds Copper/Aluminum Harnesses, Bus Bars, and Foil Laminates
- Spring Pressure Sync Mechanism Excellent response to the pressure variations prevents slip between horn and work, reduces ultrasonic energy loss and minimizes dust and waste.
- High Rigidity Pressure Mechanism
- Maintains very small deflections to ensure uniform weld side pressure.
- Unique, Original Design Ultrasonic Oscillation Frequency Automatic Tracking System Ensures stable vibration amplitude during high loads.
- High Performance Depth Control (1μm Resolution Linear Scale) Oscillation is controlled by feedback of sinking of work and work height.
- 4 Types of Oscillation Control Method Time, Work Sinking Value, Work Height, Applied Energy.
Ultrasonic Metal Welding
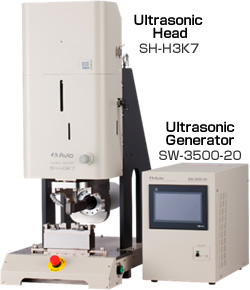
Ultrasonic metal welding method is used to join dissimilar metals of aluminum wire and copper for aluminum harnesses, thin copper alloys for vapor chambers and hoop materials, and aluminum laminated foil for rechargeable batteries
Highly Reliable Welding of Aluminum Cables to Copper Terminals
Welds Copper/Aluminum Harnesses, Bus Bars, and Foil Laminates
- Spring Pressure Sync Mechanism Excellent response to the pressure variations prevents slip between horn and work, reduces ultrasonic energy loss and minimizes dust and waste.
- High Rigidity Pressure Mechanism
- Maintains very small deflections to ensure uniform weld side pressure.
- Unique, Original Design Ultrasonic Oscillation Frequency Automatic Tracking System Ensures stable vibration amplitude during high loads.
- High Performance Depth Control (1μm Resolution Linear Scale) Oscillation is controlled by feedback of sinking of work and work height.
- 4 Types of Oscillation Control Method Time, Work Sinking Value, Work Height, Applied Energy.
Ultrasonic Welding
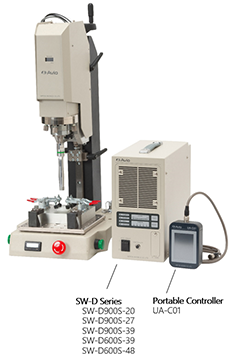
It is an ultrasonic plastic welder which utilizes ultrasonic vibration energy to perform secondary processing of plastic. It can be used not only for plastic welding but also for various purposes such as plastic caulking, fusing and cutting of non-woven fabrics, hood cutting, and packaging processing.
High-speed・automation machine type line up to support reliable “Monozukuri” (manufacturing)
SW-D series has 5 models of 20kHz~48.5kHz, 600W/900W with various control mode and monitoring function, which is applicable to wide variety of work. It is the high-end ultrasonic welder with Ethernet capability and tractability.
- The temperature rises quickly and the temperature reproducibility is good.
- Temperature profiles such as pre/main heat can be easily realized.
- Due to local heating, the heat effect to the surroundings is small.
- Since it is cooled while being pressed down, there is no unconnected due to floating.
- It does not depend on skill level of the worker.
High-frequency Induction Heater Unit
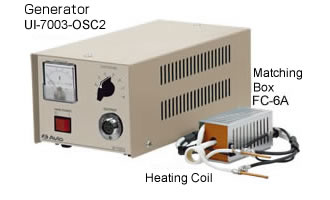
Metal Materials such as Screws or Nuts are easily Inserted into Molded Plastic Components! Induction heater units incorporate high frequency generators for non-contact heating of metal using electromagnetic induction.
- Not Only Steel but Also Brass, which is a Non-magnetic Metal, can be Heated Compatible to a Work of Φ4 - 30 mm
- Unlike the Standard Heater Method, It can Generate Heat Instantly without Pre-heating, which Contributes to Reduction of Electric Power Consumption and Prevention of Quality Change of Metal Parts
- Small Size and Light Weight is Realized by the Consolidated High Efficiency Design
- Small Diameter Cu Wire and Cu Pipe, Easy to Wind, are Used for the Heater Coil
- As the Connection between the Coil and the Matching Box is Made by a Litz Wire, Connection to an Automated Machine can be Made Easily
- By Combining with a Non-contact Type Infrared Temperature Sensor, Precision Production with the Least Variation of Torque Strength and Pull Strength can be Made
High-frequency Induction Heater Unit
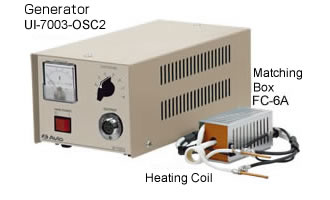
Metal Materials such as Screws or Nuts are easily Inserted into Molded Plastic Components! Induction heater units incorporate high frequency generators for non-contact heating of metal using electromagnetic induction.
- Not Only Steel but Also Brass, which is a Non-magnetic Metal, can be Heated Compatible to a Work of Φ4 - 30 mm
- Unlike the Standard Heater Method, It can Generate Heat Instantly without Pre-heating, which Contributes to Reduction of Electric Power Consumption and Prevention of Quality Change of Metal Parts
- Small Size and Light Weight is Realized by the Consolidated High Efficiency Design
- Small Diameter Cu Wire and Cu Pipe, Easy to Wind, are Used for the Heater Coil
- As the Connection between the Coil and the Matching Box is Made by a Litz Wire, Connection to an Automated Machine can be Made Easily
- By Combining with a Non-contact Type Infrared Temperature Sensor, Precision Production with the Least Variation of Torque Strength and Pull Strength can be Made